13 Mar د PCB صنعت کې د تولید لوړ پنځه وژونکي
ځینې حلونه
د فابریکې د پوړ تولیداتو اعظمي کولو لاره د پورته څخه ښکته طریقه کې ده چې په تیرو برخو کې مفصل عملیاتي ټکي په ګوته کوي. په لاندې برخو کې باید ګامونه پورته شي: د معلوماتو چمتو کول د تولید پروسې سمول د تولید پروسې چمتو کول د تولید اجرا کولو سیسټمونه د دې ټولو ننګونو لپاره تخنیکي حلونو ته اړتیا ده. او، په مهمه توګه، د راپور ورکولو سیسټمونه باید د انجینرانو، لاین آپریټرانو او د تولید مدیرانو لپاره ځای په ځای وي چې هغه ځانګړي کړنې وپیژني چې د فعالیت ښه کولو لپاره باید ترسره شي. برسېره پردې، معلومات باید په کافي وخت کې وي ترڅو د فرصت له لاسه ورکولو دمخه د ښه والي لپاره وړتیا ولري او تازه ستونزې په بل ځای کې څرګند شي. د ډیټا چمتو کول د اجزاو ماډل ان پټ او ډیزاین ډیټا ان پټ دواړو لپاره د معلوماتو چمتو کولو ته پاملرنه یو لازمي لومړی ګام دی: د اجزا ماډلینګ - تولید کونکي اړتیا لري د ټولو برخو دقیق فزیکي ماډلینګ ځای په ځای کړي چې دوی یې په لیکه کې کارولو پلان لري ، پشمول د سولډر لپاره د پن تماسونه د CAD ډیټا سره یوځای شوي. پدې کې باید شامل وي: ثابت، د CAD-کتابتون بې طرفه، د برخو ماډل کول ترڅو معیاري DFM فعال کړي او د پروسې چمتو کولو فعالیتونه لاندې. نورمال شوي اجزا آف سیٹ، گردش او قطبي بیانات یو معیار ته. د نړۍ د الکترونیکي صنعت د 750 ملیارد ډالرو پلور لري، چې دوه پر دریمه برخه یې د PCB اسمبلۍ لخوا حساب کیږي. د PCB تولید د دریو د پام وړ صنعت چلوونکو په شرایطو کې د تولید د زیاتوالي لپاره د جنون ډرایو لخوا مشخص شوی: د محصول لنډ ژوند دورې - فشار دی چې غوره محصولات رامینځته کړي او بازار ته یې راوړي مخکې لدې چې سیالۍ وکړي ، په ټیټ لګښت کې ، پداسې حال کې چې په ورته وخت کې وده کوي. د راتلونکي نسل محصول. یوازې پنځه کاله دمخه، د محصول ژوند دوره په کلونو کې اندازه شوې وه؛ اوس دوی په میاشتو کې اندازه کیږي، په ډیزاینرانو او جوړونکو فشار راوړي ترڅو د پروټوټایپ مرحلې څخه د لوړ حجم تولید ته د حرکت بهیر ګړندی کړي. ډیر پیچلتیا - جوړونکي ډیر پیچلي، د لوړ کثافت ډیزاین تولیدوي د کوچني کولو او ډیر پیچلي بورډونو سره. د PCB اسمبلۍ لپاره د موادو یو ځانګړی بیل (BOM) اوس کولی شي په مجموع کې په زرګونو برخې ولري، د سلګونو ځانګړي لاین توکو څخه جوړ شوي. "پیرودل شوي" توکي - کپیسیټرونه، مقاومت کونکي، ډایډونه او داسې نور - هر یو به یو یا څو "بدیل برخې" ولري ترڅو د لږترلږه BOM لګښت او اعظمي برخو شتون وړ کړي. د موادو ډیر پیچلي بیلونه (BOM) د اجزاو کیفیت لوړولو او غوره موندلو وړتیا باندې پریمیم لري. آؤټ سورسنګ ګړندی وده کوي - د محصول لنډ ژوند دورې او پیچلتیا ډیروالي OEMs دې ته اړ کړي چې آؤټ سورسنګ ومني ، چې اوس د PCB صنعت ترټولو ګړندۍ وده کونکي برخه ده. د الکترونیکي تولیداتو خدماتو (EMS) شرکتونو په 21 کې د بازار 2004٪ برخه درلوده، مګر د دوی ونډه به تر 30 پورې شاوخوا 2008٪ ته ورسیږي. بازار به په ټولیزه توګه په دې وخت کې یوازې 16٪ وده وکړي. د EMS چمتو کونکي ټیټ نرخونه ، بازار ته ګړندي سرعت او د غوره ترتیب بشپړولو فعالیت وړاندیز کوي ځکه چې دوی د سلګونو مختلف پیرودونکو خدمت کولو څخه ترلاسه شوي لوی راټول شوي پیرود ځواک څخه ګټه پورته کوي ، او د دوی تولیدي شتمنیو قوي کولو او د لږترلږه واحد لګښت ترلاسه کولو لپاره اداره کولو سره. د EMS چمتو کونکي د دوی د تولید او اجزاو تدارکاتو اصلي وړتیا باندې تمرکز کوي؛ OEMs وړیا دي چې د نوي محصولاتو ډیزاین او بازارموندنې تمرکز وکړي. د دې صنعت رجحانات په ښه توګه پیژندل شوي او د PCB اسمبلۍ جوړولو کې یې مرسته کړې چې په نړۍ کې یو له خورا رقابتي صنعتونو څخه دی. د لګښتونو کمولو فشار سره، پداسې حال کې چې په ورته وخت کې بازار ته د حاصلاتو او سرعت ښه کول، د فابریکې پوړ عملیاتو کې د هغو بدلونونو لټون روان دی چې کولی شي سیالي ښه کړي. په عموم کې ، د PCB اسمبلۍ عملیاتو کې 60-70٪ پانګونه شوې ثابته پانګه په ماشینونو کې د مجلس لاینونو کې بنده ده. د SMT مجلس په ځانګړې توګه د پلازمینې غښتلي دی، د بیلګې په توګه، د واحد لینونو سره چې د $ 1 ملیون ډالرو څخه ډیر لګښت لري او قیمت مخ په ډیریدو دی. د سخت فشار لرونکي تولیدي فابریکې مدیران له ځانه پوښتنه کوي چې څنګه دوی کولی شي ډاډ ترلاسه کړي چې د دوی پانګونه شوې پانګه اعظمي تولید او سیالي وړاندې کوي. ځواب نه یوازې د انفرادي ماشینونو په کچه کې دی، بلکې د بشپړ کرښې یا فابریکې پوړ په کچه هم دی. د PCB راټولونکي د تولید د فعالیت ډیری اندازه کولو څخه د محصول د محصول ځانګړتیاو څخه د دورې وخت، لاین بیټ نرخ او د لومړي پاس حاصلاتو څخه د لوړې کچې بنچمارکونو لکه "BOM تبادلې لګښت" او په کار ګمارل شوي پانګې بیرته راستنیدو لپاره ډیری اندازه کاروي. هر هغه څه چې د فعالیت کلیدي شاخصونه (KPIs) کارول کیږي، موخه یې دا ده چې د موجود اسمبلۍ لاینونو، موادو، فکسچرونو او بشري سرچینو څخه د منلو وړ کیفیت محصول اعظمي تولید تولید کړي.
- د برخو ګډوډي
- غیر موثره کرښه جوړه کړه
- د غوره وهلو نرخونو څخه ورو
- د ماشین ټیټ فعالیت
- د PCB / پروسې ترکیب فرعي غوره دی
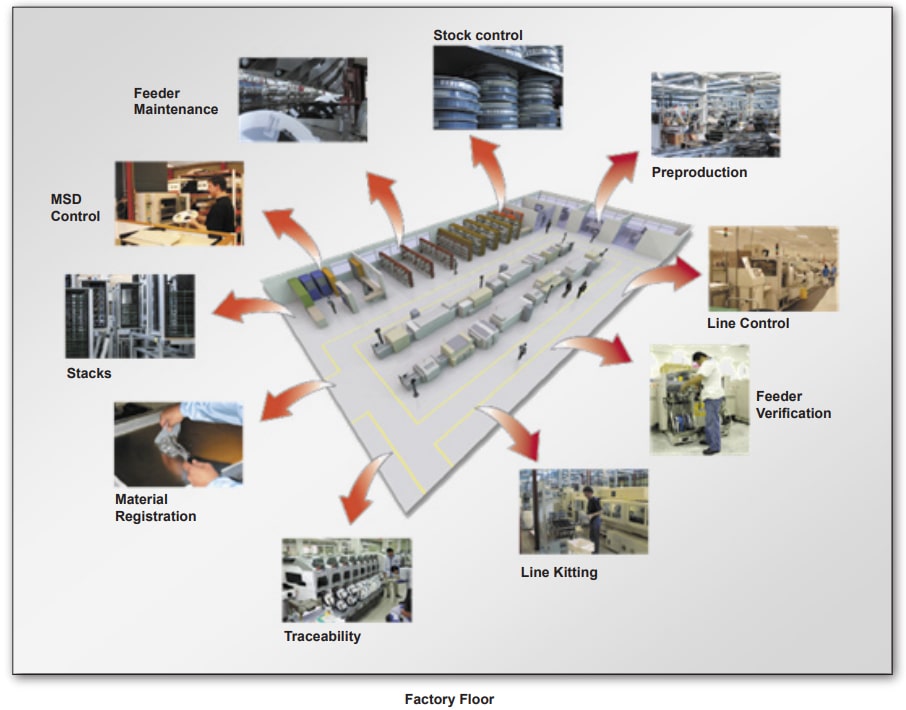
- د برخو ګډوډي لومړۍ مسله چې په تولید اغیزه کوي دا ده چې توکي په سم وخت کې په سم ځای کې ندي ، د مجلس په لیکو کې د کارولو لپاره چمتو دي. ډیری په دې باور دي چې د ټولو BOMs راټولولو لپاره د ERP یا ماسټر سټاک کنټرول سیسټم کې بشپړ پوښښ درلودل کافي دي. مګر مهم فکتور د اړتیا په وخت کې په ماشینونو کې د پرزو او موادو سم مقدار شتون او نصب کول دي. په ډله ایزه توګه د اجزاو د برخې شمیرو شتون تایید کول د فابریکې په پوړ کې د پرزو نشتوالي له امله د تولید ناکامۍ مخه نه نیسي ځکه چې:
i. هغه برخې چې دمخه یې نورو ترتیبونو ته ژمن دي - په PCBs کې د مجلس لپاره اجزا معمولا په لوی مقدار کې اداره کیږي - یا په ریلونو کې چې په زرهاو برخې لري یا په سلونو ټریو کې. که ورته برخې په ورته وخت کې د دوه تولید امرونو لپاره اړین وي، هیڅ کرښه په سمه توګه تنظیم کیدی نشي. د دې ستونزې اغیزې د سلګونو اجزاو ریلونو یا ټریونو په اوږدو کې چې د PCB عادي فابریکې پوړ کې شتون لري ضرب کول، د هر تولید امر لپاره لاینونو ته د مناسب مقدار پرزو رسولو کې د پاتې کیدو خطر زیاتوي ، سره له دې چې په مجموع کې. ، د تولید امرونو لپاره د پرزو ټول اړین مقدار د ماسټر سټاک کنټرول سیسټم کې د برخو ټول مقدار سره سمون لري.
ii. موجودې برخې نشي موندلی - ډیری وختونه، په لویو فابریکو کې، د ERP سیسټمونه مواد په سمه توګه نه تعقیبوي کله چې دوی د تولید پوړ ته خوشې شي. کلیدي معلومات - د هغې کرښې په اړه چې برخې ورته ځانګړې شوې دي، ایا هغه سیسټمونه چې دوی یې ژمن دي اوس هم په تولید کې دي، او د هغو برخو دقیق مقدار چې په دې ترتیبونو کې تړل شوي دي - په مکرر ډول ورک وي. پداسې حال کې چې موجود معلومات ښیي چې برخې د تولید پیل کولو لپاره شتون لري، دوی ډیری وختونه شتون نلري. غیر ضروري ځنډونه د تولید په پیل کې پایله لري پداسې حال کې چې "مستقیم" د ورک شوي موادو په لټه کې دي. په مساوي توګه، او د ورته لید نشتوالي له امله چې کومې برخې چیرته دي، ډیری وختونه برخې په غیر ضروري ډول یو لیک ته لیږدول کیدی شي، ترڅو د تنظیم کولو مالتړ وکړي، کله چې واقعیا د دغو برخو کافي اکمالات لا دمخه په لاین کې بار شوي وي، پاتې برخه د تولید پخوانی امر. د دې تعقیب غلطۍ د فابریکې پوړ د موجوداتو لګښت کې د غیر ضروري زیاتوالي لامل کیږي. د ځای په ځای کولو دمخه د غلط انتخاب یا نوزل ناکامۍ له امله. په لویه کچه ، دا د PCB جوړونکي د ډیر اندازې کولو په لور اړوي
iii. په قرنطین کې برخې - بل فاکتور چې د غوره کولو او ځای په ماشین کې د برخو شتون اغیزه کوي د فابریکې په پوړ کې د نورمال اتموسفیر شرایطو سره مخ کیدو لپاره د اجزاو ځینې کټګوریو حساسیت دی. ځینې وختونه اجزا د مهر شوي کانټینرونو څخه د بسته کولو وروسته د هوا د رطوبت لخوا اغیزمن کیږي او یوازې د څو ساعتونو وروسته ، دوی باید په تنور کې پخه شي ترڅو د اجزاو بدن څخه رطوبت لرې کړي. د تنور پخولو سایکلونو لخوا رامینځته شوي وقفې پدې معنی دي چې ځینې برخې د غونډې لپاره د "موجود" او "نه شتون" دورې څخه تیریږي ، حتی که دوی هر وخت په "سټاک کې" وي.
iv. د سټاک ناسم کنټرول - د ERP سیسټم کې د پرزو سټاک شتون اکثرا د غیر ثبت شوي ضایع کیدو په پایله کې غلط وي. کله چې اجزاوې د فابریکې په پوړ کې د کارولو وروسته ګودام ته راستانه شي، د ریل کې د څومره برخې پاتې کیدو دقیق انځور راټولول ستونزمن کار دی. ایا د تولید مدیران باید په ساده ډول د پیل مقدار واخلي او په BOM کې د ټاکل شوي ځای پرځای کولو شمیر کم کړي؟ شاید نه ، ځکه چې دا د ماشین سټاک کچې له لاسه ورک شوي برخې له پامه غورځوي ، چې د فابریکې په پوړ کې د راتلونکي تولید امرونو کې غیر متوقع سټاک آوټ لامل کیږي. د دې په څیر ګران (او غیر پلان شوي) تولید بندول د راتلونکو امرونو او د نیمګړتیاو سمولو لپاره د بیړني برخو پیرود لپاره له لینونو څخه د موادو پاکولو اړتیا رامینځته کوي. د سټاک ناسم کنټرول هم د ساحې پراخه لیست تفتیشونو وخت مصرف او قیمتي تمرین مجبوروي ، کله چې تولید په لازمي ډول ودرول شي پداسې حال کې چې د ERP سیسټم کې ریکارډونه په لاسي ډول د تولید پوړ واقعیت سره همغږي کیږي.
v. د سټاک کچه، د فابریکې په پوړ کې د راتلونکي تولید امرونو کې د غیر متوقع سټاک آوټ لامل کیږي. د دې په څیر ګران (او غیر پلان شوي) تولید بندول د راتلونکو امرونو او د نیمګړتیاو سمولو لپاره د بیړني برخو پیرود لپاره له لینونو څخه د موادو پاکولو اړتیا رامینځته کوي. د سټاک ناسم کنټرول هم د ساحې پراخه لیست تفتیشونو وخت مصرف او قیمتي تمرین مجبوروي ، کله چې تولید په لازمي ډول ودرول شي پداسې حال کې چې د ERP سیسټم کې ریکارډونه په لاسي ډول د تولید پوړ واقعیت سره همغږي کیږي.
- غیر موثره لاین تنظیم کول د اغیزمن SMT مجلس لاین په یو وخت کې د سلګونو ترتیب شوي متغیرونو همغږي کولو وړتیا پورې اړه لري. که د لاین ترتیب کوم اړخ غلط وي، د خراب کیفیت محصول پایله ده. د سست لاین ترتیب او ډیبګ لپاره ډیری عام لاملونه شتون لري:
i. د تنظیم کولو لارښوونې د ماشین برنامو سره سمون نه لري - په ډیری قضیو کې ، په لیکو کې د انجینرۍ ډیټا د ډیری ، منحل شوي ډیټا جریانونو څخه راځي. د هر ماشین لپاره د کیټینګ لیست د ERP سیسټم کې د BOM څخه پرمخ وړل کیږي، مګر بیا هم دا د ماشین پروګرام کونکو لخوا د BOM ویشلو او انډول کولو پریکړې په پام کې نه نیسي. د CAM سیسټمونه چې د ماشین برنامو رامینځته کولو لپاره کارول کیږي ډیری وختونه د فابریکې فرش مسافر رامینځته کولو لپاره د CAM سیسټم په پرتله د مختلف ډیټابیس څخه کار کوي. او د CAM سیسټمونه چې د AOI ماشینونو برنامه کولو لپاره کارول کیږي د هغه سیسټمونو سره توپیر لري چې د ماشینونو غوره کولو او ځای کولو لپاره کارول کیږي. د معلوماتو د جریان ټوټه کول کیدای شي پراخه وي؛ د انجینرۍ ډیټابیسونو ترمینځ د منحل کیدو هر ټکی د غونډې لینونو مختلف برخو لپاره غیر همغږي شوي ډیټا یا لارښوونې رامینځته کولو لپاره بل فرصت وړاندې کوي. د تنظیم کولو ټولې غلطۍ باید یا په سرچینه کې له منځه یوړل شي، د ډیزاین په واسطه، یا په "لومړي پړاو" کې وموندل شي او د ترتیب کولو لارښوونو ترمیمولو سره له منځه یوړل شي پداسې حال کې چې لاین ښکته او غیر ګټور وي.
ii. په ماشینونو کې د پرزو ډیټا ورک یا غلط دی - هر SMT غوره کولو او ځای کولو ماشین ، AOI ماشین او د سرکټ ټیسټر د ډیټا کتابتون ته اړتیا لري ترڅو د راټولولو ، تفتیش یا ازموینې لپاره د هرې برخې کلیدي ځانګړتیاوې تشریح کړي. یوازې کله چې د ماشین اجزا کتابتون د ډیټا څخه ډک وي چې د تولید امر لپاره اجزا تشریح کوي ماشین کولی شي خپله دنده ترسره کړي. هره نوې برخه چې د فابریکې په پوړ کې بار شوې پدې معنی ده چې د دې برخې لپاره د کتابتون ډیټا باید ماشینونو ته داخل او تصدیق شي. یوځل چې رامینځته شي ، ډاټا باید په سمه توګه اداره شي ځکه چې کوم بدلونونه چې رامینځته کیږي احتمالا د غیر ضروري کم وخت پایله کیدی شي که چیرې د وړ آپریټر لخوا ترسره نشي. د ماشین کچې برخې برخې ډیټا اداره کولو لپاره د کنټرول شوي او مرکزي حل پرته ، ډاټا باید په ډیر زحمت سره ډیری ماشینونو ته داخل شي ، د غیر ضروري ځنډیدو او د ډیری ماشینونو ترمینځ د ډیټا غیر متناسب لوړ خطر لامل کیږي.
iii. بشپړ آف لاین سیټ اپ نه دی ترلاسه شوی - ډیری جوړونکي د آفلاین اجزا بارولو او تنظیم کولو تصدیق کولو توان نلري. دا ځواکونه د تولید له پیل څخه دمخه د کار کولو لپاره چمتو شوي او تنظیم شوي چې د وخت ضایع کیدو لامل کیږي. په دې کې شک نشته چې د فیډر انوینټري ټول لګښت د آنلاین تنظیم کولو په ترسره کولو سره کم کیدی شي ، مګر د ورک شوي لاین محصول او ماشین کارولو له مخې لوړ نرخ تادیه کیږي.
iv. ترتیب په لومړي پړاو کې غلط دی - که چیرې ټولیز لاین ترتیب په پیل کې د موجوداتو چک کولو سره موازي نه وي تایید شوی، غلطی باید د لومړي بند تولید په وخت کې وموندل شي. دا د ترتیب شوي غلطۍ موندلو او له مینځه وړو لپاره خورا ګرانه لاره ده ، ځکه چې د غلطۍ رامینځته کولو او موندلو ترمینځ تیر شوی وخت اعظمي کیږي. د فیډرونو، ماشینونو، پروګرامونو د شمیر سره سم د غلطۍ / کشف / فکس فرصتونه ضرب کړئ، او د ترتیب شوي ډیبګ وخت زیاتولو فرصت روښانه کیږي، د ترتیب د هر اړخ تصدیق کولو په پرتله لکه څنګه چې ترسره کیږي. یوځل چې لومړی بند مرحله بشپړه شي او لاین په بشپړ تولید کې وي ، نو دا هم حیاتي ده چې د تیروتنې مخنیوی وشي کله چې په ماشین کې نوي برخې د ستړي شوي فیډر ډکولو لپاره ځای په ځای شي. په بدترین حالت کې، په غلطه توګه ځای پر ځای شوي برخې به د بشپړ بسته بندي کولو وروسته، د تفتیش یا ازموینې په مرحله کې کشف شي. دا ډول ترمیم ډیر لګښت لري او د نبات په ټولیز تولید اغیزه کوي.
v. د موجوده ماشین سیسټمونو څخه ګټه پورته کولو کې پاتې راتلل - د تنظیم کولو وخت کمولو غوره لاره د لاینونو ښکته کولو اړتیا له مینځه وړل دي او د تولید امرونو ترمینځ یې بیا تنظیم کول دي. د اجزاو لوی ډولونو اداره کولو پیچلتیا له امله ، فیډر ، فیډر موقعیتونه ، اجزا مقدار او هغه فاکتورونه چې د لږترلږه دورې وخت لپاره مطلوب تنظیم باندې اغیزه کوي ، ډیری تولید کونکي ټول فیډرونه او اجزا د تولید امرونو ترمینځ له لینونو څخه لرې کوي. دا کنټرول ساتي، مګر په ډراماتیک ډول تولید کموي. دمخه د تولید امرونو تحلیل کولو او د محصول ګروپونو پیژندلو سره چې کولی شي ورته سیټ اپ (یا د ترتیب اکثریت) د اسمبلۍ لاین کې شریک کړي پرته لدې چې د نه منلو وړ درجې ته د بیټ نرخ قرباني کړي ، په کم وخت کې لوی سپما ترلاسه کیدی شي. د محصول ګروپ کولو تخنیکونو کارول د لوړ مکس / ټیټ څخه متوسط حجم عملیاتونو کې د پام وړ تولیدي پرمختګونه وړاندې کوي چیرې چې بدلونونه د لاین ټیټ وخت لپاره یو له لوی مرسته کونکو څخه دی.
vi. د برخو د بیا ډکولو اړتیاو اټکل کولو کې پاتې راتلل - په لوړ حجم کې ، د ټیټ مخلوط تولید چاپیریال کې ، په بشپړ ډول د لین برنامه کولو لپاره د دقیق سمولیشن پراساس چلند لپاره د پرمختګ نشتوالی. ii. د ماشین برنامه کول د بشپړ کینیماتیک سمولیشن پراساس ندي - که چیرې د کرښې کچې سمولیشن او برنامه (انډول کول) د ماشین برنامې څخه جلا شي ، نو د دواړو ترمینځ به شخړه وي؛ توازن د انفرادي دورې وختونو په اړه دقیقو معلوماتو پورې اړه لري، او د ماشین پروګرام کول ممکن د ماشین د دورې مختلف وخت رامینځته کړي چې د لاین توازن فعالیت لخوا فرض شوي. کلیدي د هر ماشین ترتیب (فیډر، نوزل، ...) او د هغې د حرکت کینیماتیک خورا دقیق سمولیشن دی. د ماشین دورې وخت سمولو کې دقت پرته، نه یوازې د انفرادي ماشین فعالیت به زیانمن شي، بلکې په ټولیزه توګه به لاین د مطلوب ټولیز محصول لپاره متوازن نه وي. په لیکه کې د برخو د ډکولو اړتیا لیدل د ځنډیدو یوازینی مهم لامل دی. ترټولو بد حالت هغه وخت رامینځته کیږي کله چې په فیډر کې ټولې برخې ختمې شي مګر دا د لاین آپریټر لپاره د حیرانتیا په توګه راځي (څوک چې په ورته وخت کې د سلګونو فیډرونو څارنه وکړي). دا کرښه ښکته کوي پداسې حال کې چې فیډر لیرې کیږي، یو نوی ریل بار شوی (فرض کړئ چې دا په لاس کې وي)، او فیډر په ماشین کې بیرته پورته کیږي.
- د مطلوبه وهلو نرخونو څخه ورو ورو یوځل چې لاینونه تنظیم شوي وي ، تولید په خپل تکراري تال کې ځای په ځای کیږي ، سره راټول شوي PCBs د لاین بیلانس ، د ماشین وړتیاو ، او په محصول کې د ځای په ځای شوي د اصلاح کولو کچې لخوا ټاکل شوي په ثابت فریکونسۍ کې له کرښې څخه راځي. ځانګړي ماشین پروګرامونه پخپله. په دې وخت کې، تولیدات په ګرانه مګر نه لیدل شوي طریقه اغیزمن کیږي، که چیرې لینونه په اعظمي ممکنه بیټ نرخ کې د چلولو لپاره پروګرام نه وي. دا د ډیری دلیلونو لپاره پیښ کیدی شي: i. سمولیشن، د BOM ویشل/توازن کول، او د ماشین برنامه کول د بشپړ لاین په کچه نه ترسره کیږي - انفرادي ماشینونه ترټولو غوره کچې ته برنامه کیدی شي، مګر که د بشپړ کینیماتیک سمولیشن پراساس د برنامه کولو دندې ته د بشپړ لاین چلند ونه نیول شي. د ټولو ماشینونو څخه چې لاین جوړوي، په ټولیزه توګه فعالیت زیانمن کیږي، په عمده توګه د ماشین د کار بار عدم توازن له امله. د لین د دورې وخت، یا د وهلو کچه، په کرښه کې د خورا ورو ماشین لخوا ټاکل کیږي، په ټوله توګه د کرښې پروګرام کولو لپاره د سم سمولیشن پر بنسټ طریقې ته اړتیا ټینګار کوي.
ii. د ماشین برنامه کول د بشپړ کینیماتیک سمولیشن پراساس ندي - که چیرې د کرښې کچې سمولیشن او برنامه (انډول کول) د ماشین برنامې څخه جلا شي ، نو د دواړو ترمینځ به شخړه وي؛ توازن د انفرادي دورې وختونو په اړه دقیقو معلوماتو پورې اړه لري، او د ماشین پروګرام کول ممکن د ماشین د دورې مختلف وخت رامینځته کړي چې د لاین توازن فعالیت لخوا فرض شوي. کلیدي د هر ماشین ترتیب (فیډر، نوزل، ...) او د هغې د حرکت کینیماتیک خورا دقیق سمولیشن دی. د ماشین دورې وخت سمولو کې دقت پرته، نه یوازې د انفرادي ماشین فعالیت به زیانمن شي، بلکې په ټولیزه توګه به لاین د مطلوب ټولیز محصول لپاره متوازن نه وي.
iii. د ماشین په کچه د پرزو ډیټا د غوره سمبالولو فعالیت لپاره نه برنامه شوي - د هر ماشین لخوا کارول شوي د پرزو ډیټا د اجزاو اداره کولو څرنګوالی تعریفوي: په کوم سرعت سره ، په کوم نوزل سره ، د استوګنې مختلف وختونه باید څومره وي ، کوم آفسیټونه باید پلي شي. د پورته کولو نقطه او داسې نور. د لومړي بند بشپړول د دې تصدیق کولو لپاره کافي دي چې محصول په سمه توګه راټول شوی ، مګر دا د ماشین برخې ډیټا کتابتون کې د فرعي غوره سمبالولو لارښوونو له امله د کم مجلس سرعت اغیزې نه افشا کوي. یو آپریټر به ځینې وختونه د اجزاو ځای پرځای کولو سرعت کمولو لپاره غوره کړي ترڅو مجلس ډاډمن کړي ، ډیری وختونه د ساتنې مسلې ماسک کوي چې باید په ګوته شي پداسې حال کې چې د لاین عمومي تولید خورا کم کړي. لکه څنګه چې پخپله د ماشین برنامو اصلاح کول ، د فعالیت تفصيلي معلوماتو ته د لاسرسي پرته دا د انسانانو لپاره واقعیا ناممکن دي چې دا اغیزې وپیژني؛ او د کشف پرته دوی نشي سم کیدی.
- د ماشین ټیټ فعالیت د ملیونونو ډالرو په جریان کې د لینونو پانګوونې سره ، په څرګنده توګه ماشینونه باید وساتل شي ترڅو د اعظمي وخت لپاره اعظمي تولید کې ترسره شي. په هرصورت، د ماشین حالت ډیری اړخونه شتون لري چې د عمومي فعالیت په راټیټولو کې ناوړه اغیزه لري.
- د نوزل ویکیوم فشار - که دا د مشخصاتو څخه بهر وي ، نو دا د دې لامل کیږي چې اجزا د پک اپ پوائنټ او په PCB کې د دوی موقعیت ترمینځ په لیږد کې راټیټ شي.
- د چپکشی نوزل ویکیوم سویچ کول – که چیرې د ویکیوم سویچ چپکونکی وي نو د نوزلسکپس لامل کیږي. پرته له خطا د فیډر څخه اجزاو غوره کولو لپاره نوزلونو ته د ویکیوم اکمالاتو مثبت او ګړندي سویچنګ ته اړتیا ده. ورته د ځای په ځای کولو باندې تطبیق کیږي؛ د ویکیوم ورو یا غلط سویچ کول د غلط انتخاب یا ځای پرځای کیدو لامل کیږي.
- غوړ شوي تغذیه کونکي - دا د لوړې د لاسه ورکولو نرخونو لامل کیږي. د اجزاو تغذیه کونکي میخانیکي لیست کولو وسایل دي چې د وخت په تیریدو سره اغوندي. لکه څنګه چې میکانیزم د عادي استعمال سره اغوستل کیږي، د اخیستلو لپاره د اجزا وړاندې کولو دقت کمیږي، چې په سمه توګه په غوره کولو کې د ناکامۍ لامل کیږي، کوم چې د اجزاو او سایکل وخت ضایع کوي. iv. د ساتنې ضعیف لارښوونې - د SMT لینونه په هر ساعت کې د لسګونو یا سلګونو زرو برخو په نرخونو کې برخې ځای په ځای کوي. د دې بریښنا ماشین سرعت د کمیدو فعالیت مشاهده کول ستونزمن کوي. مس پکونه د لیدلو لپاره خورا ګړندي پیښیږي ، مګر په تکراري فعالیت کې د څو ملی ثانیو ځنډ د توقیف شوي فعالیت لامل کیږي. د دقیق او وخت خبرتیا پرته چې د فعالیت کمښت چیرته دی، د لاین آپریټرانو او د ساتنې پرسونل د فعالیت لوړولو لپاره د سم ګام پورته کولو لږ چانس لري.
- د ساتنې ضعیف لارښوونې - د SMT لینونه په هر ساعت کې د لسګونو یا سلګونو زرو برخو په نرخونو کې برخې ځای په ځای کوي. د دې بریښنا ماشین سرعت د کمیدو فعالیت مشاهده کول ستونزمن کوي. مس پکونه د لیدلو لپاره خورا ګړندي پیښیږي ، مګر په تکراري فعالیت کې د څو ملی ثانیو ځنډ د توقیف شوي فعالیت لامل کیږي. د دقیق او وخت خبرتیا پرته چې د فعالیت کمښت چیرته دی، د لاین آپریټرانو او د ساتنې پرسونل د فعالیت لوړولو لپاره د سم ګام پورته کولو لږ چانس لري.
- د بریښنا ماشین سرعت د کمیدو فعالیت مشاهده کول ستونزمن کوي. مس پکونه د لیدلو لپاره خورا ګړندي پیښیږي ، مګر په تکراري فعالیت کې د څو ملی ثانیو ځنډ د توقیف شوي فعالیت لامل کیږي. د دقیق او وخت خبرتیا پرته چې د فعالیت کمښت چیرته دی، د لاین آپریټرانو او د ساتنې پرسونل د فعالیت لوړولو لپاره د سم ګام پورته کولو لږ چانس لري.
- د PCB / پروسې ترکیب فرعي غوره PCBs ډیزاین کیدی شي ترڅو د مجلس پروسې دوستانه یا د پروسې دښمني وي. ډیری PCBs په نهایت کې راټول کیدی شي ، مګر د فرعي غوره ډیزاین له امله د اړتیا څخه لوړ لګښتونه ، د بیا کار کولو کچه او د لاین موثریت د ډیزاین ځانګړتیاو په پایله کې توپیر لري لکه:
i. PCB ماشین یا لاین دوستانه نه دی - فیډیشیلز پټ دي، اجزا د لیږدونکو سره په ټکر کې دي، د مجلس پینل ډیزاین د اصلاح کولو لپاره دوستانه ندي. د ډیزاین محدودیتونه لکه په تخته کې د اجزاوو ویش، یا په BOM کې ډولونه، داسې دي چې یو ډول ماشین نشي کولی د ټیټ ځای پرځای کولو لګښت ترلاسه کړي او دا تر هغه وخته نه لیدل کیږي چې محصول په لیکه کې چلوي.
ii. د سولډر سټینسیل ډیزاین د فرعي غوره سولډر جوڑوں لامل کیږي - دا د لوړ بیا کار پایله ده. د مجلس لومړنی هدف د باور وړ سولډر جوائنټونه رامینځته کول دي. د سولډرینګ پروسې باندې د ښه کنټرول سربیره ، د اجزاو پن ، پیډ - پیټرن او سولډر - سټینسیل اپرچر ترکیب باید غوره شي ترڅو پروسې ته د هغه بندونو ترلاسه کولو غوره چانس ورکړي چې د منلو وړ زغم کې وي (په عموم ډول په لسګونو ضعیف جوڑوں کې اندازه کیږي ، هر ملیون تولید شوی).
iii. د PCB ډیزاین ترتیب کمان او مرحلې هڅوي - د مجلس لپاره په لاین کې بار شوي د PCBs پینل باید په بشپړ ډول فلیټ وي ، ترڅو په ماشینونو کې د لیږدونکي "هنګ اپ" او پروسس کولو غلطیو څخه مخنیوی وشي. په ټولو محورونو کې د مسو د مساوي ویش سره د PCB ډیزاین کولو سره، د پروسس کولو په جریان کې د PCB د رکوع او مرحلې تمایل به کم شي.
iv. د پیډ/ټریک نمونې د بیا جریان په جریان کې د قبرونو کښت هڅوي - د کوچني غیر فعال چپ اجزاو په لور د تمایل سره ، لکه د 0201 کڅوړې اوس په حجم کې اداره کیږي ، د پیډ او ټریک نمونو ډیزاین ترڅو د اجزا په دواړو اړخونو کې مساوي تودوخې ډوبیدو اغیزو ته اجازه ورکړي. د زیاتوالي اهمیت. لکه څنګه چې اجزا روښانه کیږي، د ریفلو په جریان کې د سطحې فشار اغیزې خورا مهم کیږي؛ که چیرې یو اړخ د بل څخه مخکې تیریږي، د سطحې فشار کولی شي د ګډ وچ اړخ د پورته کولو لامل شي، چې د "قبر ډبرې" اغیز رامینځته کوي.
ځینې حلونه
د فابریکې د پوړ تولیداتو اعظمي کولو لاره د پورته څخه ښکته طریقه کې ده چې په تیرو برخو کې مفصل عملیاتي ټکي په ګوته کوي. په لاندې برخو کې باید ګامونه پورته شي: د معلوماتو چمتو کول د تولید پروسې سمول د تولید پروسې چمتو کول د تولید اجرا کولو سیسټمونه د دې ټولو ننګونو لپاره تخنیکي حلونو ته اړتیا ده. او، په مهمه توګه، د راپور ورکولو سیسټمونه باید د انجینرانو، لاین آپریټرانو او د تولید مدیرانو لپاره ځای په ځای وي چې هغه ځانګړي کړنې وپیژني چې د فعالیت ښه کولو لپاره باید ترسره شي. برسېره پردې، معلومات باید په کافي وخت کې وي ترڅو د فرصت له لاسه ورکولو دمخه د ښه والي لپاره وړتیا ولري او تازه ستونزې په بل ځای کې څرګند شي. د ډیټا چمتو کول د اجزاو ماډل ان پټ او ډیزاین ډیټا ان پټ دواړو لپاره د معلوماتو چمتو کولو ته پاملرنه یو لازمي لومړی ګام دی: د اجزا ماډلینګ - تولید کونکي اړتیا لري د ټولو برخو دقیق فزیکي ماډلینګ ځای په ځای کړي چې دوی یې په لیکه کې کارولو پلان لري ، پشمول د سولډر لپاره د پن تماسونه د CAD ډیټا سره یوځای شوي. پدې کې باید شامل وي: ثابت، د CAD-کتابتون بې طرفه، د برخو ماډل کول ترڅو معیاري DFM فعال کړي او د پروسې چمتو کولو فعالیتونه لاندې. نورمال شوي اجزا آف سیٹ، گردش او قطبي بیانات یو معیار ته.
No Comments